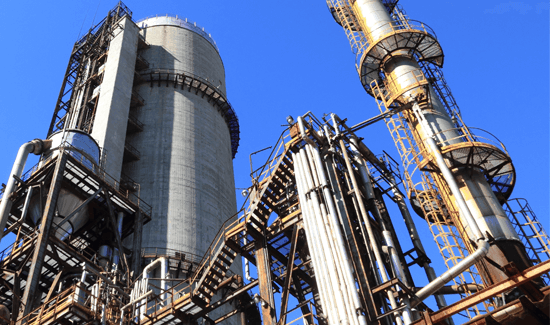
Reliability describes the ability of a system or component to function under stated conditions for a specified period of time. Quantitative reliability assessments can be performed at various stages of an asset's life cycle: conceptual, preliminary and detailed design phases, production/ construction phase, operation phase, etc.
- Functional Safety Assessment (FSA) - Safety Integrity Level (SIL) Assessment and Verification and Development of Safety Requirement Specification (SRS)
- Process Hazard Analysis (PHA) - Hazard & Operability (HAZOP) and Hazard Identification (HAZID), Quantitative Risk Assessment (QRA), Failure Mode Effect Analysis (FMEA), Event Tree Analysis (ETA), Fault Tree Analysis (FTA) and Markov Analysis.
RELSAFE has the competence to perform Reliability Studies such as:
- Reliability, Availability and Maintainability (RAM) Studies - Failure Mode, Effects and Criticality Analysis (FMECA), Planned Maintenance Optimization (PMO) and Availability Prediction
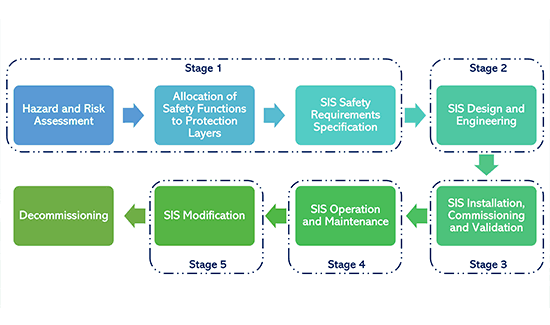
Functional Safety Assessment (FSA)
Safety Instrumented Systems (SIS) are designed and used to prevent or mitigate hazardous events to protect people or the environment or prevent damage to process equipment. ‘Functional Safety Assessment (FSA)’ is carried out to ensure that the SIS continues to provide the correct level of risk reduction via appropriate maintenance, operation and modification controls, including procedures and safe systems of work.
Safety Integrity Level (SIL) refers to the risk reduction to a tolerable quantifiable level. It is a ‘risk based approach’, which emphasizes on the need for risk reduction with the aid of SIS.
Following Functional Safety Assessments (FSA) can be performed for instrumented systems and components in any industrial facility:
- SIL Assessment – This study is required to determine the SIL requirements for Safety Instrumented Functions (SIF). This involves determining the necessary risk reduction required to meet the tolerable risk for specific hazardous scenarios.
- Safety Requirement Specification (SRS) – The development of SRS is an important activity during the design of SIS performing safety instrumented functions (SIF). SRS shall specify all requirements of SIS needed for detailed engineering and process safety information purposes.
- SIL Verification – This study demonstrates if the SIS meets the requirements of particular SIL level identified by SIL assessment study.
RELSAFE uses state-of-the-art standards IEC 61508 (Functional safety of electrical/ electronic/ programmable electronic safety-related systems) and IEC 61511 (Functional Safety – Safety Instrumented Systems for the process industry sector) for performing SIL assessment, SRS and SIL verification studies.
IEC standards specify the risk assessment and measures to be taken in the design of safety instrumented systems (SIS) comprising of sensor, logic solver and actuator. These measures include ‘fault avoidance’ (systematic faults) and ‘fault control’ (systematic and random faults).
Information on various stages of an industry’s safety life cycle where SIL studies are necessary is illustrated in the image.
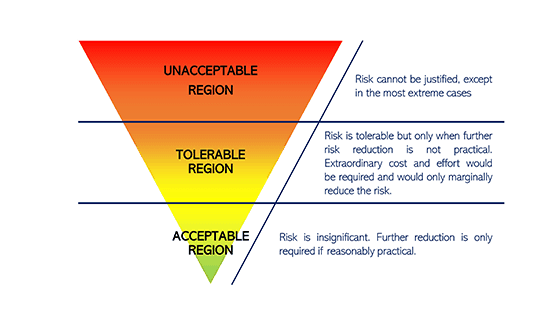
Safety Integrity Level (SIL) Assessment
SIL assessment studies are performed using various techniques such as Calibrated Risk Graphs, Semi-Quantitative Layers of Protection Analysis (LOPA) and Fully-Quantitative Fault Tree Analysis (FTA). This study basically deals with determination of necessary risk reduction required to meet the tolerable risk for specific hazard scenarios.
A SIL assessment study typically involves:
Determination of potential frequency and consequence of any specific hazard.
Determination of the risk reduction obtained by other measures and the resultant risk gap.
Assignment of SIL requirements for safety instrumented functions (SIF) based on resultant risk gaps, in accordance with IEC 61508 and IEC 61511.
RELSAFE has the capabilities to conduct a workshop on ‘SIL Assessment’ and provide recommendations based on client specific risk criteria or requirements and tailored solutions based on a Cost Benefit Analysis that can ensure As Low As Reasonably Practicable (ALARP) risk from the industrial facility.
Development of Safety Requirement Specification (SRS)
SRS is required to identify and present the safety requirements for the safety instrumented functions (SIFs) to fulfill the requirements of IEC 61511.
The requirements need to be documented during the planning stage. SRS is developed after the hazard/risk analysis and allocation of safety functions to protective layers in the safety life-cycle (as per IEC 61511-1) are performed. The requirements are divided into three components: (a) General requirements, (b) Functional requirements and (c) Safety Integrity requirements.
RELSAFE has the competence to conduct a workshop on 'Development of SRS’ and perform a study on ‘Development of SRS’ for different SIFs as per client’s needs.
SIL Verification
SIL verification study helps to assess the SIL of any specific safety instrumented functions (SIFs) using different methods like: Fault Tree Analysis (FTA), Reliability Block Diagrams (RBD) and Failure Mode Effects and Criticality Analysis (FMECA).
This study is generally performed following SIL assessment and SRS studies to determine if the SIFs identified in the LOPA analysis meet their respective target SIL.
RELSAFE has the competence to provide following services:
- Assessment on the random hardware reliability and the fault tolerance of each SIF. SIF includes the input sensors, logic modules and actuators (final elements) using RBD.
- Assessment on the Probability of Failure on Demand (PFD) and Safe Failure Fraction (SFF) of the existing or proposed SIFs in the facility using RBD, FTA and FMECA;
- Recommendations on SIF (and SIS) following a SIL assessment, SRS and SIL verification studies.
Process Hazard Analysis
Process Hazard Analysis (PHA) is a set of organized and systematic assessments of potential hazards associated with any industrial process. Generally, a PHA is directed towards analyzing all potential causes and consequences of hazards in a facility like fire, explosions, releases of toxic or flammable chemicals or even major spills of hazardous material. The primary focus of such a study will be on equipment, instrumentation, utilities, human actions, and external factors that will have an impact on the safety of the facility.
A PHA should address various risks and their consequences on the safety of facility including possible hazards in the facility, records of any previous incident in the facility that has a likelihood potential for hazardous consequences, consequences of failure of process systems and engineered safety systems in the facility and human errors.
Since PHAs will be performed for the entire facility, the team performing the study should include process safety experts, engineers, operators, supervisors and other employees who will have knowledge of facility, safety, codes and regulations that are applicable to the process being analysed.
There are many methods to perform a PHA such as Hazard & Operability study (HAZOP), Hazard Identification study (HAZID), Quantitative Risk Assessment (QRA), Bow-Tie Analysis, What-If Analysis, etc.
HAZOP & HAZID Studies
HAZOP study is performed to review the design of any process industry or facility, to identify and analyse the design and engineering issues that were not identified earlier. The primary objectives of a HAZOP study includes: (a) identifying potential hazards in the system and (b) identifying potential operability problems with the system and in particular identifying causes of operational disturbances and production deviations likely to lead to non-conforming products.
The overall complex design of any facility is broken down into smaller and simpler “nodes” which are then reviewed for their operational risk and reliability. There are many different tools and techniques available for the identification of potential hazards and operability problems such as Checklists, Failure Mode and Effects Analysis (FMEA) and Fault Tree Analysis (FTA).
HAZID study is a qualitative technique for the early identification of potential hazards. The objective of this study is to identify potential hazards and reduce the probability and consequences of hazards on any facility.
This study is a combination of identification, analysis and brainstorming by the HAZID team members. Guidewords are used in order to identify possible potential and hazardous effects as well as threats. Furthermore, the team analyses the appropriate controls that should be put in place to prevent or control each identified threat. RELSAFE can perform HAZOP and HAZID studies for any industrial facility, with a multi-disciplinary team having an overall view/ perspective on the risks and possible hazards.
Quantitative Risk Assessment (QRA)
For any process industry, Quantitative Risk Assessment and Availability Analysis principles are useful. QRA are mainly carried out, (a) at the design stage to compare the reliability of different design options as an aid to decision making, and (b) at the operational stage for identification of existing design weak links, operation and maintenance procedural weaknesses, common cause failure mechanisms and human interventions and human error probabilities, to identify dominant contributors to system/plant unavailability, to identify and prioritize improvement measures, to optimize operation, surveillance testing and maintenance (allowed outage time), to carry out cost-benefit analysis for any improvement measure and to have an aid for risk informed decision making.
There are many methods to perform a QRA, which includes,
- Fault Tree Method: This is an advanced technique being used widely in many of the process industries for modelling the systems/plant as a whole for risk assessment/operational performance and availability assessment.
- Event Tree Method: This method is used to postulate different hazard scenarios possible in an industry/facility and to find out quantitatively the contribution of each scenario (i.e. probability) to the overall risk from the industry/facility.
- Monte Carlo Simulation Method: This method is used in the availability/risk assessment when reliability parameters are represented by some distributions.
- Markov’s Model: This method is used to effectively compute the availability of a system when the system has different states of operation.
- Fault tree analysis includes not only all the combinations of component failure modes that could result in system/plant unavailability but also all dependencies between components in terms of common cause failures (both explicit and implicit), human errors, component testing aspects, operation and maintenance procedural aspects and preventive and corrective maintenance un-availabilities all in one single model.
- This model helps to directly arrive at measures for maintenance optimisation, provides insights on the dominant contributors to plant unavailability, importance of component un-availabilities in a ranked way to prioritise O&M activities.
- The advantages of Fault Tree Analysis for the complete process are many which are being used worldwide to support cost benefit decisions in all industries.
All the above methods can be used in combinations or in a standalone manner depending on the type and extent of assessment required.
RELSAFE can perform a QRA study (i.e. an overall plant risk assessment). This includes identification of potential hazard/risk scenarios by a combination of qualitative and quantitative methods, analysing the risk potential and contribution of each scenario to overall risk by QRA methods like fault tree and event tree methods using RiskSpectrum®, providing prioritised solutions for managing risk or for improvement of safety of the plant.
Reliability, Availability and Maintainability (RAM) Study
Reliability, Availability and Maintainability (RAM) are attributes associated with any system design that has substantial impact on the performance of an engineered system.
In RAM modelling,
- Reliability is the probability of success of function of a system or the frequency of its failures.
- Availability is the proportion of time a system is in a functioning state/condition.
- Maintainability is a measure of the ease with which a system can be maintained or brought to a functioning state/condition following a failure.
RAM study is a structured analysis of the performance of a system to meet its deliverability/demand. It is a quantitative analysis of a complete system/parts of a system/sub-system. RAM analysis is important for asset owners to ensure that existing and future assets are designed and operated in an optimized way.
Purpose of RAM study is to: (a) obtain an estimate of the expected system performance, (b) identify dominant contributors to system unavailability/production loss, (c) evaluate various measures to improve system performance, (d) plan maintenance and manage spares inventory and (e) provide inputs during evaluation of life cycle cost.
RELSAFE uses state-of-the-art ISO 20815 (Petroleum, petrochemical and natural gas industries – Production assurance and reliability management) for providing services related to RAM studies.
A typical RAM study will provide the following outputs:
- Overall availability (system availability/production availability/deliverability) and component-wise availability;
- Insights on available and consumed resources/spare parts; and
- Recommendations to improve reliability, availability and maintainability of systems and components
Outputs from a RAM study can be used for optimized performance of the facility including product optimization, design optimization, spares management philosophy, maintenance planning and inputs for financial analyses and decision support.
RELSAFE can perform Reliability, Availability and Maintainability Studies using various state-of-the-art methods and techniques like FMEA/FMECA, Fault Tree Analysis (FTA), Reliability Block Diagrams (RBDs) and Common Cause Failure analysis.
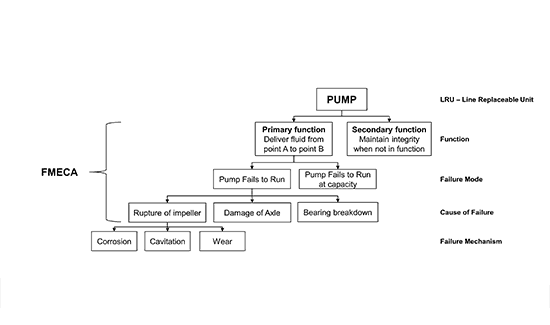
FMECA
FMECA is a risk analysis method used to identify failure modes for the components, and the corresponding failure causes. This study forms a cornerstone of RAM analysis. It is used to identify the consequence of the failure modes on sub-systems (local) and the total system as a whole (global) and how the failure modes can be detected.
The identified failure modes are ranked in a risk matrix. The critical consequences are related to downtime/production loss and hence further analysed in RAM analysis.